Water Filling Machine
Water filling machines are used to fill liquid products, such as water, juice, soda and other beverages into bottles. They often incorporate rinsing, filling, and capping functions into a single automated process, ensuring efficiency and hygiene standards are met. Water filling machines are crucial in maintaining product quality, minimizing contamination risks, and optimizing production throughput in water bottling plants.
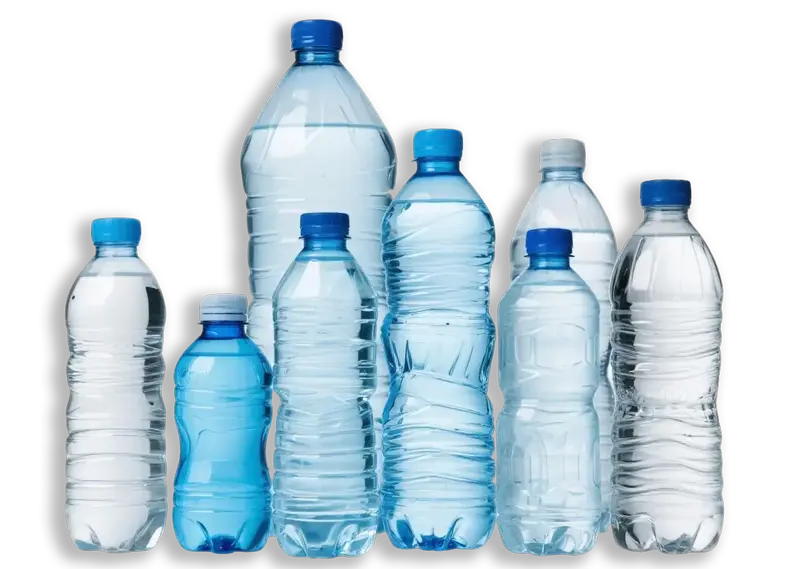
Benefits of Water Filling Machine
Consistency
Water filling machines can ensure that every bottle is filled with the same amount of product with minimal to no error. They work in a cycle where every product is dispensed precisely based on volume, weight, level, and other input measurements.
A solution to plastic pollution
One of the most significant environmental advantages of water filling machines is their ability to reduce plastic waste. These machines allow companies to fill reusable, recyclable containers with water, eliminating the need for single-use plastic bottles.
Increase production speed
The water filling machine can fill several more containers. The filling speed depends on the filling head of the machine and the viscosity of the liquid. On average, a machine with 16 filling heads can reach a speed of 120 bottles per minute, which can complete thousands of bottles of filling per day.
Filling versatility
Water filling machines don’t just bottle the same kind of product in the same type of container. When settings are adjusted, these bottling machines can fill any kind of product in any specific measurement. These machines are able to fill both thick and thin liquids, which benefits businesses with multiple lines of production looking for this industrial versatility feature.
Four Common Filling Methods for Water Filling Machine
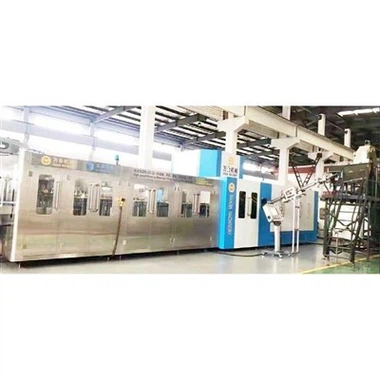
Atmospheric filling method
Atmospheric pressure filling method refers to atmospheric pressure, relying on the liquid’s own weight into the packaging container, the entire filling system is in an open state of work, atmospheric pressure filling method is the use of a liquid level to control the filling.
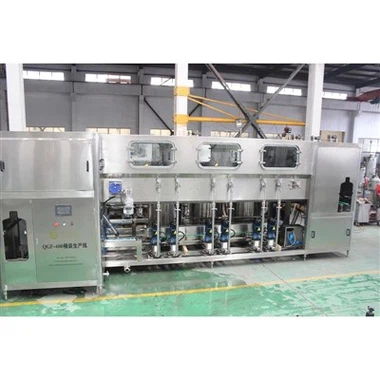
Isobaric filling method
The isobaric filling method is to use the compressed air in the upper air chamber of the storage tank to fill the container first so that the pressure in the storage tank and the container is close to equal. In this closed system, the liquid substance flows into the container through its own weight. It is suitable for inflating liquids.
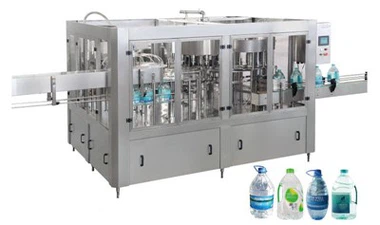
Vacuum filling method
The vacuum filling method is to uses the pressure difference between the liquid being filled and the exhaust port to suck out the gas inside the container for filling. The pressure difference can make the flow of the product greater than the equal pressure filling. It is particularly suitable for filling small mouth containers, viscous products, or large-capacity containers with liquids.
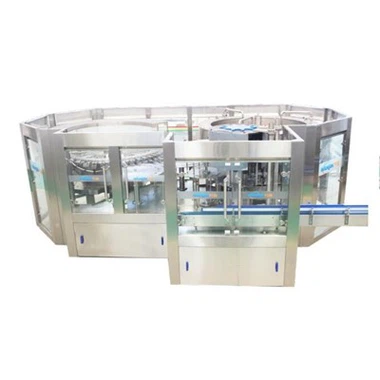
Pressure filling method
The pressure filling method is the opposite of the vacuum filling method. The can sealing system is at a higher than atmospheric pressure, with positive pressure acting on the product. Liquid or semi-fluid liquids can be filled by pressurizing a reserved space at the top of the storage box or by using a pump to push the product into the filling container. The pressure method keeps the pressure at both ends of the product and the vent above atmospheric pressure and has a higher pressure at the end of the product, which helps to keep the CO2 content of some drinks low. This pressure valve is suitable for filling products that cannot be vacuumed.
FAQ
The water filling machine operates on the principle of liquid pressure filling. When the pressure is high, the liquid flows into the bottle using its own weight. This process occurs when the pressure of the liquid reservoir matches the volume of air present in the bottle.
Bottles per minute (BPM) is a common measure for determining how fast a water filling machine can actually fill bottles. The measurement is a simple equation, with a few variables. For automatic machinery, it can be determined by the number of fill heads times the number of cycles run per minute.
Consider the nature of your product and its impact on the machine type. For instance, a dense or thick liquid requires specific machinery like piston fillers to manage consistency efficiently. Next up are receptacle specifications. You will need precise nozzles that cater to bottles with narrow openings seamlessly.
Water filling machines can fill various types of containers, including plastic bottles, glass bottles, and aluminum cans. They can handle different shapes and sizes, from small single-serve bottles to large gallon containers, by adjusting the machine settings or using different attachments.
Common filling methods include gravity filling, where the water flows into the container by gravity; pressure filling, which uses pressure to force water into the container; and vacuum filling, which uses a vacuum to draw water into the container.
Capacities can vary widely, from small machines that fill a few hundred bottles per hour to large industrial machines capable of filling tens of thousands of bottles per hour. The capacity depends on the specific model and the requirements of the production line.
Hygiene is maintained through regular cleaning and sanitization of the machine, especially the parts that come into contact with water. Many machines have CIP (Clean-In-Place) systems that automatically clean and sterilize the internal components.
Most water filling machines are designed to be versatile and can be adjusted to handle different bottle sizes and shapes. This is typically done through adjustable components, such as conveyor guides, filling nozzles, and capping mechanisms, allowing the machine to accommodate various container dimensions.
Factors include the machine’s design and capacity, the type of filling method used, the viscosity of the liquid, the size and shape of the containers, and the efficiency of the rinsing and capping processes. High-speed machines are designed for large-scale production and can fill thousands of bottles per hour.
Advantages include increased production efficiency, consistent and accurate filling volumes, reduced labor costs, improved hygiene and safety, and the ability to handle various container types and sizes. Automation also minimizes human error and contamination risks.
Filling volume is controlled using sensors and control systems that monitor the amount of water dispensed into each container. This can be achieved through time-based control, flow meters, or weight-based systems, ensuring each container receives the exact volume required.