Carbonated Drink Filling Machine
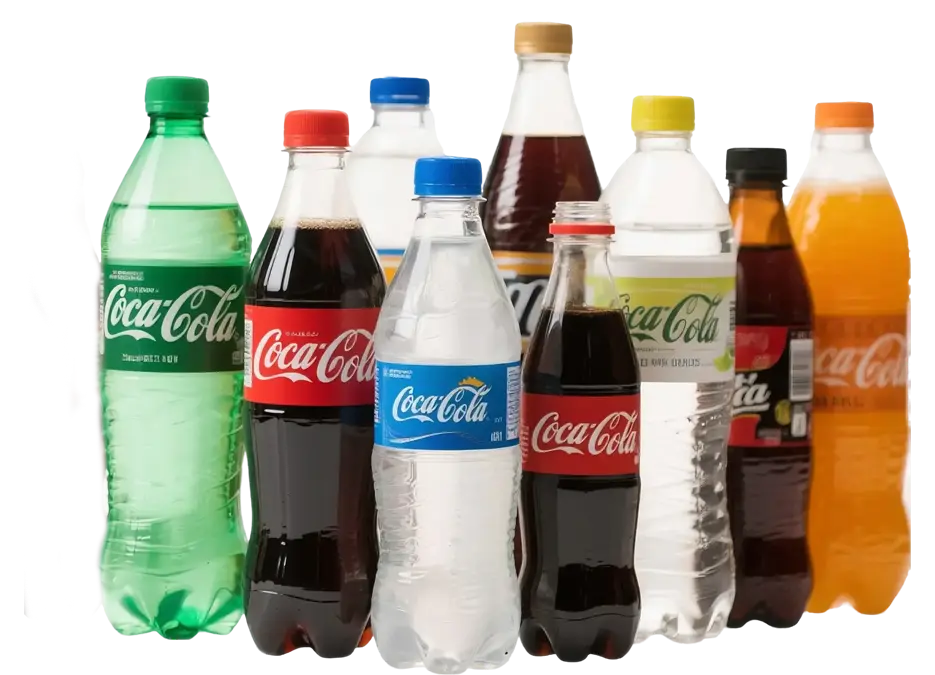
Benefits of Carbonated Drink Filling Machine
Maintains CO₂ Levels and Fizz
Designed to fill under pressure, these machines prevent carbonation loss during bottling, ensuring the drink retains its intended fizz and taste all the way to the consumer.
Pressure-Resistant and Foam-Free Filling
Equipped with isobaric filling valves, the system fills bottles smoothly without foaming or overflow—crucial for high-speed production and maintaining product quality.
Integrated Rinsing, Filling, and Capping
Typically built as a 3-in-1 monoblock machine, it automates the entire process—bottle washing, carbonated filling, and capping—saving space and improving hygiene.
High-Speed, Efficient Production
Optimized for mass production, these machines can fill thousands of bottles per hour, making them ideal for soda, sparkling water, energy drinks, and beer production lines.
Why Choose Our CSD Filling Machines?
Preserving Carbonation
Advanced CO2 retention technology ensures the perfect level of carbonation in every bottle or can, providing consistent quality for consumers.
Customization
Our machines are customizable to fit your production requirements, from bottle sizes to labeling integration and CIP systems.
Expert Support
We offer full support, including installation, training, and after-sales services, to ensure a smooth operation.
FAQ
The water filling machine operates on the principle of liquid pressure filling. When the pressure is high, the liquid flows into the bottle using its own weight. This process occurs when the pressure of the liquid reservoir matches the volume of air present in the bottle.
Bottles per minute (BPM) is a common measure for determining how fast a water filling machine can actually fill bottles. The measurement is a simple equation, with a few variables. For automatic machinery, it can be determined by the number of fill heads times the number of cycles run per minute.
Consider the nature of your product and its impact on the machine type. For instance, a dense or thick liquid requires specific machinery like piston fillers to manage consistency efficiently. Next up are receptacle specifications. You will need precise nozzles that cater to bottles with narrow openings seamlessly.
Water filling machines can fill various types of containers, including plastic bottles, glass bottles, and aluminum cans. They can handle different shapes and sizes, from small single-serve bottles to large gallon containers, by adjusting the machine settings or using different attachments.
Common filling methods include gravity filling, where the water flows into the container by gravity; pressure filling, which uses pressure to force water into the container; and vacuum filling, which uses a vacuum to draw water into the container.
Capacities can vary widely, from small machines that fill a few hundred bottles per hour to large industrial machines capable of filling tens of thousands of bottles per hour. The capacity depends on the specific model and the requirements of the production line.
Hygiene is maintained through regular cleaning and sanitization of the machine, especially the parts that come into contact with water. Many machines have CIP (Clean-In-Place) systems that automatically clean and sterilize the internal components.
Most water filling machines are designed to be versatile and can be adjusted to handle different bottle sizes and shapes. This is typically done through adjustable components, such as conveyor guides, filling nozzles, and capping mechanisms, allowing the machine to accommodate various container dimensions.
Factors include the machine’s design and capacity, the type of filling method used, the viscosity of the liquid, the size and shape of the containers, and the efficiency of the rinsing and capping processes. High-speed machines are designed for large-scale production and can fill thousands of bottles per hour.
Advantages include increased production efficiency, consistent and accurate filling volumes, reduced labor costs, improved hygiene and safety, and the ability to handle various container types and sizes. Automation also minimizes human error and contamination risks.
Filling volume is controlled using sensors and control systems that monitor the amount of water dispensed into each container. This can be achieved through time-based control, flow meters, or weight-based systems, ensuring each container receives the exact volume required.