Blowing System
Servo system is applied in the machine to achieve synchronized control of the whole system, realizing the integrating control and manufacture of each unit. As a result, efficiency of the production can be enhanced, investment can be reduced, and energy consumption and maintenance cost can be lowered as well.
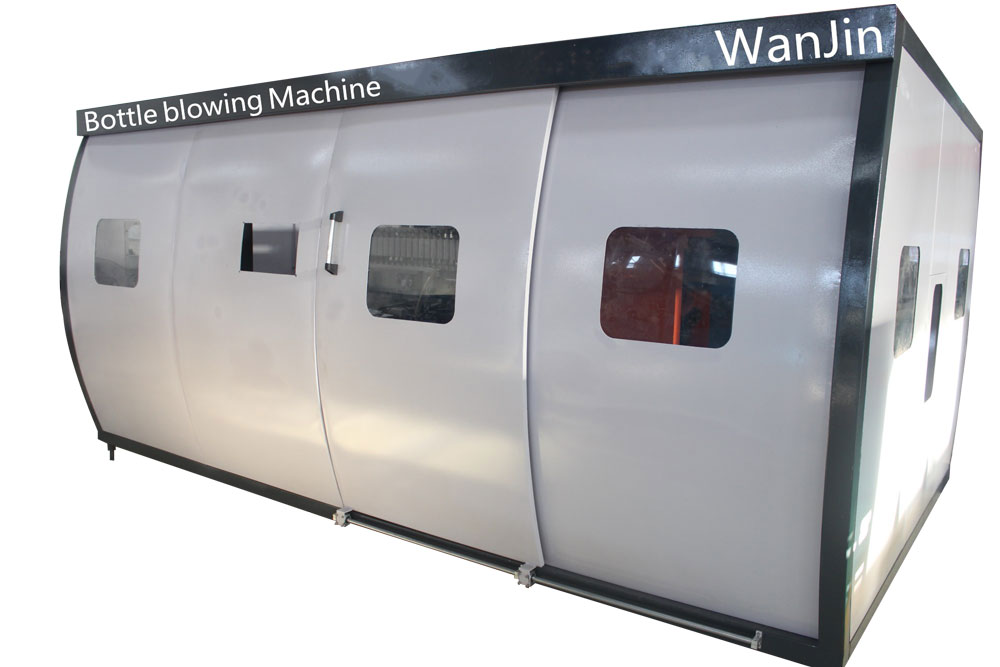
Benefits of Automatic Bottle Blowing Machine
Versatility
Automatic PET bottle blowing machines can produce bottles in various shapes, sizes, and designs, making them suitable for a wide array of products. This versatility is a significant advantage for manufacturers serving diverse markets.
Cost-Efficiency
PET is an economical and recyclable material, making it a cost-effective choice for bottle production. Automatic PET bottle blowing machines efficiently utilize this material, reducing production costs.
High Productivity
These machines offer high production rates, capable of producing a large number of bottles per hour. This increased productivity allows manufacturers to meet market demands efficiently.
Consistency and Quality
Automatic PET bottle blowing machines deliver consistent bottle quality and wall thickness. This reliability ensures that the final product meets the highest quality standards, which is crucial for customer satisfaction.
What to Consider When Choosing Automatic PET Bottle Blowing Machine
1.Production capacity
The production capacity of the PET bottle blowing machine is one of the most critical factors to consider when selecting the right machine for your business needs. It determines the number of bottles the machine can produce in a given period. A machine that can produce the required number of bottles within your desired production period should be selected. It is crucial to consider the future growth of your business when selecting a PET bottle blowing machine. Choose a machine that can accommodate future growth in production capacity.